Efficient Spare Parts Management is Crucial – Here are Tips on How OEMs Can Optimize It
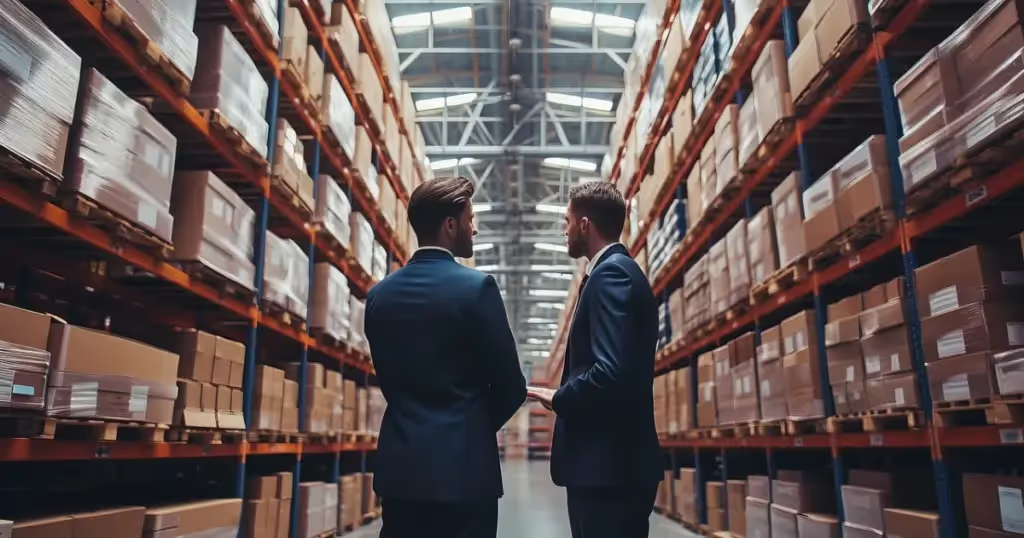
- Across industries, heavy machinery will experience downtime – it’s just a matter of when.
- OEMs and their partner dealers have a responsibility to act fast or ideally predict in advance when a machine needs service, providing spare parts instantly to enable machine uptime.
- Poor spare parts management can result in machine downtime, business disruption, financial loss, and damage to a brand’s reputation.
- Optimize spare parts planning with the IoT, predictive analytics, inventory management systems, staff training, and solid supplier relationships.
What is Spare Parts Management
Spare parts management is more than a back-end OEM priority; it has major implications in the real world. If machinery involved in food packaging or preparation goes down, the business has a number of hours or days before that food becomes a total loss. If farming equipment experiences downtime during harvest season, an entire year’s worth of work can be jeopardized. When construction equipment needs a spare part, any delays in getting that spare part can push the project timeline back significantly.
In any industry that relies on heavy machinery to get the job done, there is so much at stake. These businesses rely on OEMs, dealers, and the entire aftermarket ecosystem to optimize spare parts planning, ensuring machine uptime and efficiently propelling operations. If OEMs and their partners fail to rectify equipment malfunctions quickly, the losses can be astronomical.
But don’t worry, with proper preparation and proactive spare parts planning, those losses can be avoided. Whether you are leading an OEM business, working as a partner dealer, or involved in the supply chain process at all, understanding spare parts planning can save the day.
Why Does Efficient Spare Parts Planning Matter?
In a situation where a spare part is needed for a certain service, there are essentially two ways things can go. Imagine you’re a farmer that is operating during harvest season. You have only a limited period of time to collect the crops that have been growing for a year under your care. One day one of your machines, or more, stops working.
Here’s what might happen in a situation where poor spare parts planning is in play:
- You contact your parts dealer and ask if they can help you repair the machine. You’re not sure what is wrong with it, so they send out a servicer to assess the issue.
- The servicer identifies the issues, finds the spare part that needs to be replaced, and reaches out to the dealer to see if that spare part is in stock.
- Because of poor planning, the part availability isn’t ideal, and you have to wait two weeks before the dealer can get you the part you need.
- All the crops you have been spent a year cultivating, and protect from pests won’t be collected in time and will result in lost revenue.
- The whole chain of food distributors and end customers won’t receive your product and will have to look elsewhere.
What can connectivity do for your business
On the flip side, if OEMs and dealers have worked together to optimize spare parts management, the situation might look like this:
- When you call the dealer, they send out an expert to look at the machine.
- The expert identifies the necessary part and lets the dealer know.
- Because the dealer prioritized dealer parts planning, they have a few of those parts on hand and deliver it to your warehouse that same day.
- The machine service repairman replaces the part and gets your operations off the ground that very same day.
- End customers will receive the product on time, your organization maintains its reputation and avoids financial roadblocks.
When any organization’s operations are disrupted due to machine downtime – whether it’s a farm, a contractor, or a manufacturer – it’s up to dealers, OEMs, and other supply chain experts to illustrate effective spare parts management. Without that, downtime can be disastrous in more ways than one.
Consequence of Inefficient Spare Parts Management
In worst-case scenarios, the consequences of inefficient spare parts management can be far-reaching for businesses, their customers, and downstream members of the supply chain. The negative impacts of poor spare parts planning can manifest in a number of ways:
- Downtime: Machine downtime can reduce production efficiency, require costly workarounds, or halt operations entirely. Downtime is a major risk for businesses that use heavy machinery, and with poor spare parts management by OEMs and their partners, instances of downtime are higher in frequency and impact.
- Increased Costs: For automotive manufacturers, the average cost of production line downtime is $22,000 per minute. Without proper spare parts planning, companies can lose hundreds of thousands of dollars every day.
- Reduced Satisfaction: It’s not just businesses that lose when machines go down – customers lose, too. Reduced customer satisfaction due to product delays or quality changes can result in high customer turnover, damaging a business’s reputation and brand loyalty.
- Lost Sales: If a customer has to go somewhere else to source a product because their normal supplier is in the midst of an outage, the costs of downtime are exacerbated by the lost sales piled on top.
Downtime is one issue, but bad parts planning is another issue entirely. If downtime arises, every entity -- from OEMs to dealers – needs to be prepared to quickly rectify the situation. Ensuring part availability, providing fast repair services, and using predictive analytics to reduce downtime in the first place can rid the supply chain of the consequences of poor parts planning.
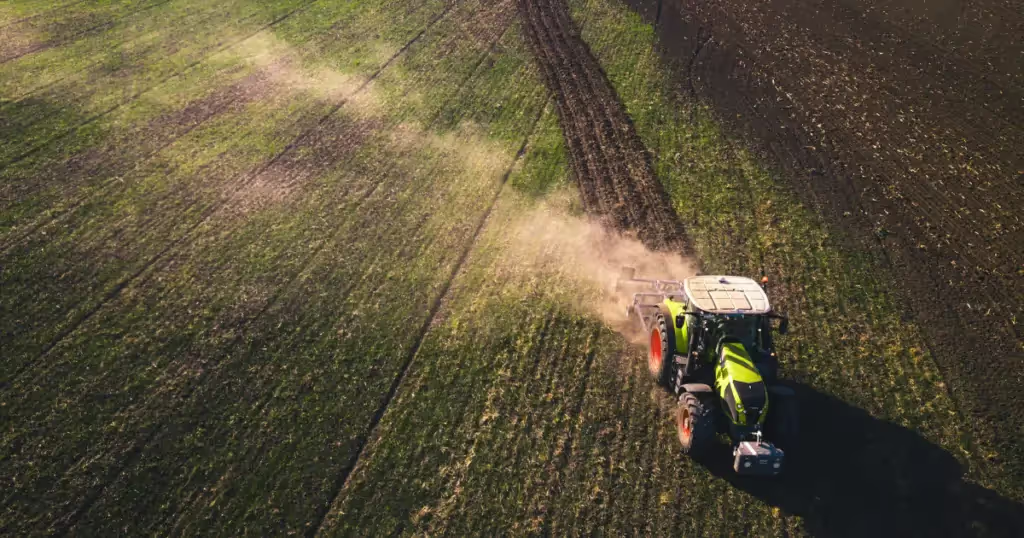
Benefits of Efficient Spare Parts Planning
When done well, spare parts management doesn’t just reduce the negative impacts of machinery issues; it can actually bring a number of benefits to the forefront for businesses, technicians, and customers alike:
Business Benefits of Efficient and Proactive Spare Parts Planning
- Increased Revenue: When OEMs and dealers work diligently in the background to anticipate their customers’ machinery needs and ensure part availability, those businesses can maintain production, ensure output, and reach revenue growth goals more effectively.
- Reduce Costs: As mentioned above, downtime is costly. If a part isn’t available, the costs associated with downtime grow by the minute. Instead, when a spare part is easily accessible, downtime is decreased, bringing costs down as well.
- Efficiency Boost: In a situation where every second matters, spare parts management boosts production efficiency. By being able to lean on OEMs and dealers to react quickly or proactively solve a problem before downtime occurs, machinery-dependent businesses will see greater efficiency across the board.
Technician Benefits of Efficient and Proactive Spare Parts Planning
- Less Time Wasted: When a technician heads to a business to repair a machine, if they have the spare part in hand, the fix is simple and fast. If they have to go out to the client’s facility, identify the necessary part, then wait days for the dealer to supply it, they will have wasted a lot of unnecessary time.
- Enhanced Productivity: One of the key metrics to customer satisfaction is technician productivity. Are they able to use spare parts to solve machinery issues quickly? If so, the technician will be more productive, and the customer will be happier in the end.
Customer Benefits of Efficient and Proactive Spare Parts Management
- Faster Service: Going hand-in-hand with the enhanced productivity of the technician, when part availability is prioritized, customers get serviced faster, enabling them to revert to a fully functional production state.
- Higher Satisfaction: Equipment malfunctioning comes with the territory in many industries, but when parts are replaced with ease and care, customers will see their experience with OEMs, dealers, and technicians as positive. It’s not about avoiding issues entirely – it’s about being ready to solve them when they arise.
- Downtime Reduction: Downtime can cripple a business. The lost revenue and additional costs can cause cash flow issues, damage operations, and have long-lasting business implications. With optimized dealer parts planning, downtime is reduced, and issues are avoided.
Challenges in Dealer Parts Planning
As crucial as spare parts management is, it’s not an easy thing to perfect. OEMs and dealers are tasked with some of the most complex responsibilities in the supply chain, and spare parts management might just top the charts. Today, supply chains are more advanced – but also more complex – than ever. If OEMs want to deliver exceptional service to their end users, they need to understand the following:
Supply Chain Complexity
Supply chains are no longer the simple, linear flow of goods from a production-based entity to a customer. Today, supply chains are hyperconnected, meaning that information, data, and even goods can be part of a bi-directional flow between OEMs and the businesses they serve. This evolution comes with a lot of benefits, but when it comes to spare parts planning, today’s supply chain intricacies can make it hard to properly manage spare parts planning.
Customers Have Different Demands
One agricultural customer could have a tractor malfunction that requires one part, and another agricultural customer could have the same tractor malfunction due to a different part entirely. Customers’ needs vary widely, and with the machinery used today, the number of parts that may need to be replaced or fixed is more diverse than ever. Dynamic customer needs can be hard to manage if OEMs, dealers, and their partners aren’t prepared for every scenario.
Accurate Solutions are the Only Solutions
If equipment malfunctions, no business has time to troubleshoot a bunch of solutions or test out different parts replacements. Accuracy is the only option; technicians need to be able to diagnose a problem, get the correct part from the dealer, and replace it with ease. Otherwise, customers will adapt their supply chain to partner with different OEMs, dealers, and technicians.

5 Tips for Optimizing Spare Parts Management
Spare parts management is difficult, but not impossible. With the right practices and technologies, dealers and OEMs can work together to ensure part availability, deliver replacement parts quickly, and reduce downtime for their customers. Here are 5 tips for optimizing spare parts management:
Utilize Retail Inventory Management Systems
The complexity of managing spare part inventory should never be underestimated. If you’re tracking things in outdated spreadsheets or using paper mechanisms, switch to a sophisticated retail inventory management system like ClearOps. Our system gives detailed visibility to stock levels, allows users to make replenishment orders in minutes, and provides deep insights into demand forecasting.
Harness the Power of the IoT
With technology-enabled machines, the Internet of Things can be used to accurately assess where certain parts are, alert service teams of potential parts issues, and even suggest the optimal approach to replacing the part. The IoT can detect malfunctions early, sometimes before they lead to downtime, paving a path for truly getting in front of an issue before it happens.
Tap into Predictive Analytics for Forecasting
Predictive analytics are a superpower that most OEMs and dealers haven’t fully tapped into yet. With Artificial Intelligence and Machine Learning Models, OEMs can anticipate needs based on historical trends, industry news, and more. When you can more accurately predict where and when parts will be needed, it’s a lot easier to ensure part availability for your end users.
Invest in Staff Training
Even the best technologies in the world can’t replace well-trained staff members. Are your technicians continuously educated on how to identify machinery malfunctions and address them? Do dealer staff have an understanding of what happens to the end user if downtime goes beyond a few hours or days? Everyone needs to have visibility to every part of the supply chain when it comes to spare parts management.
Build Strong Supplier Relationships
In a situation where a spare part isn’t available and you need to get it ASAP, do you have the relationships with your suppliers that enable you to call in a favor or a rush order? Strong supplier relationships can often turn into the one thing that saves the day when all else has failed – don’t overlook them.
Make It or Break It with Spare Parts Management
Even if Original Equipment Manufacturers (OEMs) supply top-of-the-line products in the first place, OEMs and their partner dealers have to be ready for machinery malfunctions throughout the entirety of the equipment’s life cycle. If one of those malfunctions happens – and it will – being prepared with optimal spare parts management is key.
By using technology to garner predictive insights, enabling machines with the IoT, and relying on advanced systems like ClearOps to get in front of equipment malfunctions, downtime can be mitigated. Less downtime leads to better output, higher revenue, lower costs, and happier customers. Spare parts planning is one of the most crucial elements for all OEMs; if you’re not ready for the unknown, you’re not ready to work within today’s supply chain ecosystem.
FAQs
What is the purpose of spare parts management?
The purpose of spare parts management is to ensure that the necessary components are available when needed to maintain and repair equipment and machinery. This helps to minimize downtime, optimize operational efficiency, and reduce costs.
What is spare parts planning?
Spare parts planning is the process of forecasting, scheduling, and managing the procurement and inventory of spare parts required for the maintenance and repair of equipment and machinery. This process ensures that the necessary parts are available when needed, minimizing downtime and optimizing operational efficiency.
What is spare parts philosophy? Spare Parts Philosophy refers to the strategic approach and principles governing the management, acquisition, storage, and distribution of spare parts within an organization. It encompasses various aspects aimed at ensuring the availability of necessary components to maintain operational efficiency and minimize downtime. What is the scope of spare parts management?
The scope of spare parts management encompasses a wide range of activities and processes aimed at ensuring the availability, optimal use, and effective control of spare parts within an organization.
The purpose of spare parts management is to ensure that the necessary components are available when needed to maintain and repair equipment and machinery. This helps to minimize downtime, optimize operational efficiency, and reduce costs.
Spare parts planning is the process of forecasting, scheduling, and managing the procurement and inventory of spare parts required for the maintenance and repair of equipment and machinery. This process ensures that the necessary parts are available when needed, minimizing downtime and optimizing operational efficiency.
Spare Parts Philosophy refers to the strategic approach and principles governing the management, acquisition, storage, and distribution of spare parts within an organization. It encompasses various aspects aimed at ensuring the availability of necessary components to maintain operational efficiency and minimize downtime.
The scope of spare parts management encompasses a wide range of activities and processes aimed at ensuring the availability, optimal use, and effective control of spare parts within an organization.
We want you to succeed!
Maximize your success in a decentralized dealer network with our comprehensive guide.
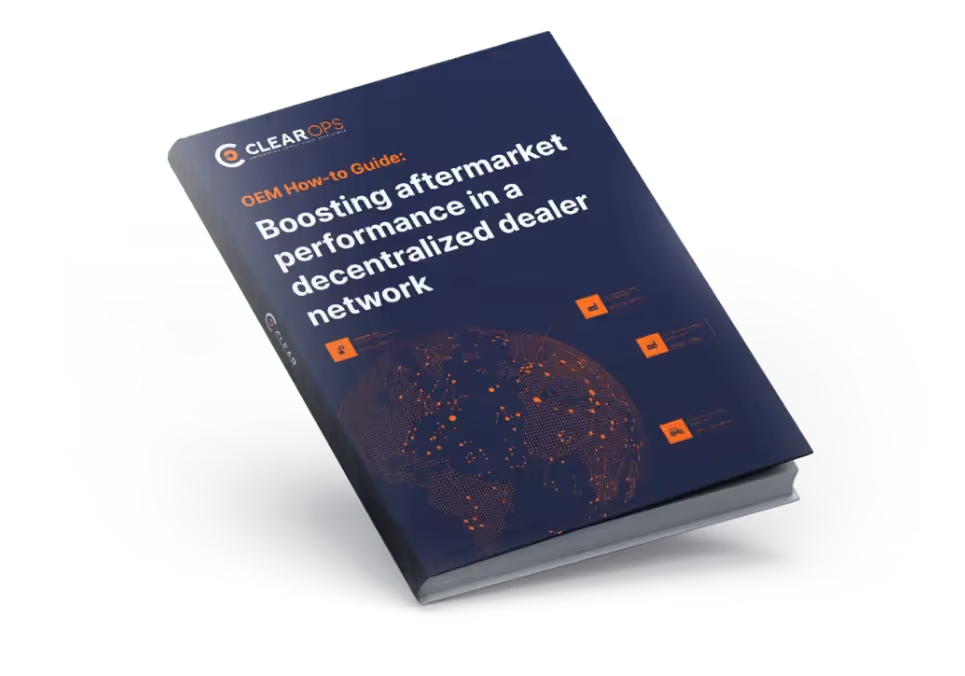
Book your free demo!
Get in contact with us today - see your Aftersales Success tomorrow.
ClearOps is an aftersales platform that enables collaboration between manufacturers, dealers and end customers.
We are already trusted by the world's leading manufacturers and over 8000 associated dealers.